ACCUEIL |
PHOTOS
GRES |
PHOTOS
FAÏENCES |
TOURNAGE
MOULAGE |
EMAILLAGE |
CUISSON |
|
Enfournement |
Courbes |
Four
électrique |
Four
à
Gaz Induit |
Four
à
Gaz Pulsé |
Réfection
four
électrique |
Régulation |
Défournement |
|
LIENS |
.......... |
|
PRESENTATION DU FOUR
A GAZ
|

FOUR
A GAZ A AIR PULSE 1300°C 40L
(
Plaque d'enfournement 300mm x 200mm sur 450mm de haut )
|
|
-
Bruleur
à air pulsé.
Un
four à air pulsé n'utilise pas la convection
naturelle pour son fonctionnement,
l'air et le gaz sont injectés sous pression par le bruleur.
Le four est étanche
et en légère surpression, les gaz de combustion
sortent du four par le bas à l'horizontal,
un tube en inox fait office de cheminé. La fonction de la
cheminée est
d'aspirer les gaz de combustion avec de l'air froid pour les
évacuer en
hauteur à une température plus basse. Dans le cas
de cuisson en réduction le CO
brule dans le bas de la cheminée au contact de
l'air.
Le
four est alimenté par deux bouteilles de propane de 13
Kg reliées à un
détendeur à pression fixe de 37 mbar.
Cette pression
est régulée par une vanne motorisée
pour
définir le débit de gaz qui traverse le gicleur
de 2mm de
diamètre.
L'air sous pression est fourni par une turbine
de pistolet
de peinture passe pression, pour ne par trop solliciter la turbine elle
est
alimentée en 110V par l'intermédiaire d'un
transformateur. La pression en entrée de la vanne de
régulation motorisée est de 220 mbar. Le
débit est
défini par la surface des fentes par lesquelles passe l'air
pour provoquer le tourbillon de la flamme.
A
l'entrée du bruleur la pression de l'air et du gaz est
réglable de 0.5 à 20 mbar,
à pression égale le four est en cuisson neutre.
Pour une cuisson en oxydation
la pression d'air est maintenue plus haute que la pression du
gaz, la
puissance du bruleur est déterminé par le
débit de gaz. Pour diminuer la
température de la flamme il est possible d'augmenter le
débit d'air, ce mode de
fonctionnement est utilisé en début de cuisson
pour que la température du four
ne monte pas trop vite. Pour une cuisson en réduction la
pression doit rester
plus haute que la pression d'air, en réduction le rendement
de la combustion
est plus basse pour maintenir la puissance du bruleur le
débit de gaz doit être
plus important qu'en oxydation. Les cuissons en réduction
produisent du CO qui
est un gaz mortel, à haute température le CO
brule dans l'air mais il est
difficile de garantir sa destruction à 100%. Pour limiter le
risque le four est
à l'extérieur, il est
protégé de la pluie par un avant toit, le gaz,
l'air
et les prises de mesures pour la régulation
arrivent en souterrain.
Pour
éviter les explosions causées par l'accumulation
du gaz dans le four le
brûleur est toujours allumer avec la porte ouverte. Le plus
simple pour allumer
le four sans risque est de jeter un morceau de coton imbibé
d'alcool enflammé
dans le bruleur puis d'ouvrir l'air et le gaz.
En
bas du four un trou avec un bouchon permet de voir
l'intérieur du four
pendant la cuisson, il est ainsi possible de voir tombé des
montres
pour
vérifier la température de cuisson. Un
deuxième trou équipé d'un tube en
alumine est équipé d'un thermocouple
relié au boitier de régulation.
|
 |
|
-
Régulation
du bruleur
|
 |
Boitier
de régulation avec les fonctions suivantes :
- Mesure
de température du four
- Mesure de pression d'air
- Mesure de pression du gaz
- Calcul du débit de gaz pour gérer la courbe de
monté
- Calcul du débit d'air pour contrôler
l'atmosphère
- Pilotage des servomoteurs des vannes
|
Vannes
de régulations qui alimentent le bruleur
avec :
- Vannes
de gaz
- Vanne d'air
- Deux servomoteurs
- Gicleur de débit minimum d'air
- Gicleur de débit
minimum de gaz
- Bielles pour les réglages min et max
|
|
 |
|
CONSTRUCTION DU FOUR
|
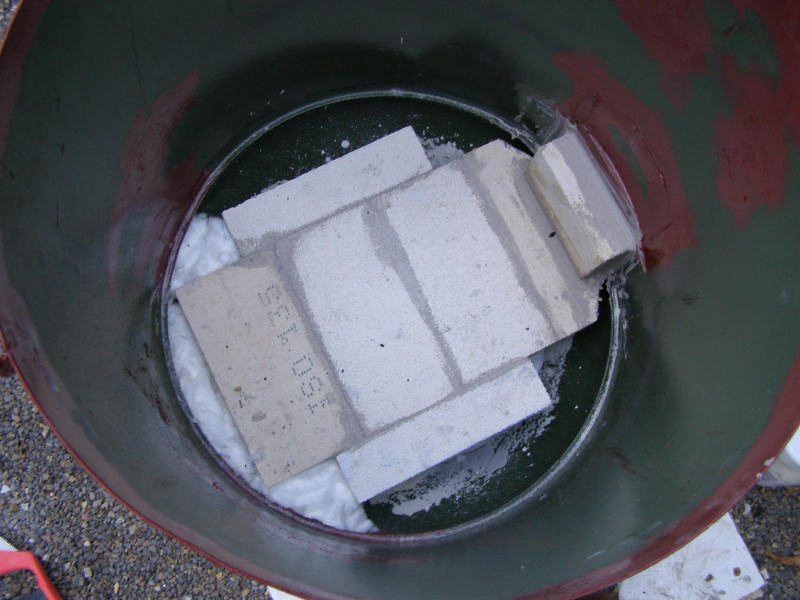
Structure
métalique et fond en brique.
La
carcasse du four est une cuve de chauffe-eau, des tubes de
30x30mm soudé
à l'arc forment les pieds. Les dimensions
extérieures sont: hauteur 700mm (plus pieds 200mm),
diamètre 500mm.
La
carcasse de la porte est faite avec le haut de la cuve du chauffe-eau
du tube 20x20mm soudé permet de
réaliser l'articulation de la porte et
la poignée. Deux ressorts fixés sur la porte
limite la force d'ouverture.
Les
briques en fond de four doivent supporter le poids de la charge, elles
assurent le passage du bruleur et la sortie des gaz de combustion.
Les briques sont taillées pour épouser le fond de
la
cuve, une mince couche de ciment permet un bon calage des briques pour
qu'elle ne se casse pas avec la charge.
Les angles morts sont comblés avec de la fibre
céramique pour une bonne isolation.
|

Isolation
extérieure du four en fibre céramique
Deux
Couches de fibre sont plaquées sur la tole exterieure.
|

Isolation
intérieure en fibre rigide.
Les
plaques de fibre sont découpées pour s'imbriquer,
les
plaques sont emboitées en force. A la première
cuisson
les matériaux haute température on toujours du
retrais.
Des trous sont faits sur la plaque de fond pour le passage des quilles
et du bruleur.
|

Cheminée
du four.
Un
trou est fait dans les briques pour réaliser le
départ de la cheminée en bas du four.
Le
tube
en acier inox utilisé pour faire la cheminée est
fixé aux deux tubes
arrière qui font office de pied et d'articulation pour la
porte.
Protéger
efficacement l'acier de la corrosion avec
un bon antirouille, pendant la cuisson l'eau
dégagée par les poteries
sous forme de vapeur traverse les couches
d'isolations et se condense
sur la face intérieure des tôles du four.
|
 |
|
ISOLATION DU FOUR
-
Choix
de l'isolation
Il
existe 4 caractéristiques principales à regarder
pour choisir un isolant:
- La résistance à la
température
- Le pouvoir isolant
- La
capacité thermique spécifique (pouvoir d'un
matériau à emmagasiner la chaleur)
- Le prix.
En règle générale les
matériaux qui résistent bien à la
température (1300°C)
sont cher et peut isolant, les matériaux avec une faible
capacité thermique (légers)
et un bon pouvoir isolant ne résistent pas aux hautes
températures.
La capacité thermique ne doit pas être
négligée, dans un four une grande partie
de l'énergie consommée est absorbée
par l'isolation du four pendant la monté en
température et restituée au cours du
refroidissement. Ce phénomène donne de l'inertie
au four, il est long à chauffer et consomme plus.
Une isolation multicouche est plus performante, elle permet
de choisir
différents matériaux en fonction de la
température
qui décroit dans
l'isolation de l'intérieur vers l'extérieure du
four.
-
Calcul
de l'isolation
Différence de température
en °C entre les 2 faces d'un mètre carré
d'isolant pour le passage d'un watt :
R
(m².°C/W)
= Epaisseur (m) /
Conductivité thermique (W/mK)
Pour calculer le R
d'une isolation multicouche additionner les R de chaque
épaisseur d'isolant.
Pour un four à gaz qui monte à
1250°C R doit se
situer entre 0.5 et 0.7
Puissance perdue par un mètre carré
d'isolation à la température maximale du four en
régime stabilisé:
P perte
(watt/m²) = (Température
de la face interne (°C) - Température de la
face externe (100°C)) / R
Puissance perdue par les 6 faces du four
à la
température maximale en régime
stabilisé:
P perte totale
(watt) = ( P perte
face 1(watt/m²) x
Surface face
1(m²)) + ( P perte face 2(watt/m²) x
Surface face 2(m²)) + ....
Pour un R à 0.6 et une température dans le four
de
1300°C la perte par m² d'isolation est de 2000W.
Pour que le
four monte sans peine à sa température maximale
la
puissance des brûleurs doit être le quadruple de
celle des
pertes pour une cuisson en oxydation.
Différence de température entre les deux faces de
chaque couche d'isolant à la température maximale
du four en régime stabilisé:
T
(°C) = R de la couche
(m².°C/W) x
P perte (watt)
Pour trouver la température maximale à la
quelle chaque couche
d'isolant est soumise soustraire les différences de
températures en
partant de
la température de la face interne.
Matériaux
d'isolation |
Prix |
Masse
volumique |
Température
max
d'utilisation |
Conductivité
thermique(W/mK) |
|
€/dm³ |
(Kg/m³) |
°C |
à
500°C |
à
1000°C |
à
1200°C |
Tole
inox |
25 |
7800 |
300 |
30 |
x |
x |
Laine
de roche HT |
0.2 |
200 |
550 |
0.10 |
x |
x |
Béton
cellulaire |
0.15 |
350 |
600 |
0.15 |
x |
x |
Vermiculite |
2.6 |
400 |
900 |
0.21 |
x |
x |
Silicate
de calcium |
2 |
250 |
1000 |
0.10 |
0.17 |
x |
Brique
légère (type
26) |
2.8 |
900 |
1450 |
0.26 |
0.38 |
0.45 |
Brique
légère (type
23) |
2.3 |
550 |
1250 |
0.20 |
0.26 |
0.30 |
Isolant
microporeux |
15 |
250 |
1000 |
0.03 |
0.05 |
x |
Board
1000°C (fibre rigide bio) |
3.8
|
320 |
1000 |
0.12 |
0.20 |
x |
Board
1300°C(fibre rigide bio) |
5.4
|
360 |
1300 |
0.12 |
0.23 |
0.3 |
Board
1450°C(fibre rigide Toxique) |
6.2 |
290 |
1450 |
0.10 |
0.20 |
0.25 |
Fibre
céramique 1100°C |
1.2 |
220 (comprimée) |
1100 |
0.16 |
0.35 |
x |
Fibre
céramique 1300°C |
1.3 |
130 (comprimée) |
1300 |
0.15 |
0.36 |
0.5 |
Fibre
céramique 1400°C (Toxique) |
2
|
130 (comprimée) |
1280 |
0.13 |
0.28 |
0.41 |
(Valeurs variables en fonction des fournisseurs)
-
Montage
de l'isolation (multicouche)
Les matériaux doivent être
coupés avec précision avec une
scie égoïne ou un cutter pour ne pas avoir de trou
à l'assemblage, s'il reste
des trous boucher les avec une patte réfractaire ou de la
fibre.
La couche
extérieure de l'isolation et installée en premier
sur la sole et les cotés avec une
légère pression
et en quinconce pour immobiliser les
différents panneaux. Pour la sole attention au poids que
doivent supporter les
isolants, ajouter des "pieds" en briques légères..
-
Isolation
de mon four à gaz à air pulsé
2 mm
de
tole acier
50
mm de fibre céramique 1100°C
30
mm de fibre céramique rigide 1300 °C
TOTAL
= 80 mm
|
|
 |
|